I. Material structure and production process
(I) Monocrystalline silicon solar panels
The material structure of monocrystalline silicon solar panels is based on a single, complete crystal structure, with silicon atoms arranged in a highly ordered lattice. This orderly arrangement gives monocrystalline silicon excellent electrical properties and lays the foundation for efficient photoelectric conversion. Its production process is complex. First, high-purity silicon materials need to be melted at high temperatures, and then monocrystalline silicon ingots are grown by the Czochralski method or the Float Zone method. In the Czochralski method, after a seed crystal contacts the molten silicon, it is slowly pulled up and rotated, and silicon atoms are deposited layer by layer on the seed crystal in an orderly manner to form a monocrystalline silicon ingot. The Float Zone method uses the heat generated by a high-frequency coil to locally melt the silicon rod, and achieves crystal growth by moving the heating zone. Finally, the monocrystalline silicon ingot is cut into thin slices, and after a series of processing, it is made into a monocrystalline silicon solar panel.
(II) Polycrystalline silicon solar panels
Polycrystalline silicon solar panels are composed of a random combination of multiple tiny single crystals, and there are grain boundaries between the crystals. Although this structure affects the migration efficiency of electrons to a certain extent, it also gives polycrystalline silicon unique advantages in production process and cost. The production of polycrystalline silicon adopts the ingot casting method. After the silicon material is heated to a molten state, it is poured into a mold of a specific shape and cooled and solidified to form a polycrystalline silicon ingot. Compared with the growth process of single crystal silicon, the ingot casting method does not require precise control of the crystal growth direction. The process is relatively simple, the production efficiency is higher, and the material utilization rate is also higher, thereby reducing production costs.
II. Performance
(I) Photoelectric conversion efficiency
Due to the high integrity of its crystal structure, monocrystalline silicon solar panels are less hindered in the process of electron migration and have a higher photoelectric conversion efficiency. At present, the conversion efficiency of commercial monocrystalline silicon solar panels is usually between 20% and 23%, and the highest efficiency in the laboratory has exceeded 26%. Due to the existence of grain boundaries, electrons in polycrystalline silicon solar panels easily interact with impurities and defects at the grain boundaries during migration, resulting in energy loss. The conversion efficiency is generally between 17% and 20%, and the highest efficiency in the laboratory is about 22%. Under the same lighting conditions and area, monocrystalline silicon solar panels can generate more electricity, which makes it have obvious advantages in projects with limited land resources or high power generation requirements.
(II) Weak light response capability
In weak light environments, monocrystalline silicon solar panels perform better than polycrystalline silicon solar panels. Monocrystalline silicon has a uniform crystal structure and high electron mobility, and can maintain a high power generation capacity even in the early morning, dusk or cloudy days when the light intensity is low. However, due to the large number of impurities and defects at the grain boundaries of polycrystalline silicon, the charge recombination loss is large under weak light conditions, resulting in a significant decrease in power generation. This feature makes monocrystalline silicon solar panels more suitable for use in areas with complex lighting conditions or short lighting time.
(III) Temperature coefficient and hot spot effect
Temperature has an important influence on the performance of solar panels. The temperature coefficient of monocrystalline silicon solar panels is relatively low, generally between - 0.3%/°C and - 0.4%/°C, which means that when the temperature rises, the decrease in its power generation efficiency is relatively small. In high temperature environments, monocrystalline silicon solar panels can maintain relatively stable performance. The temperature coefficient of polycrystalline silicon solar panels is relatively high, about - 0.5%/°C, and the power generation efficiency decreases more significantly under high temperature conditions. In addition, the crystal structure of monocrystalline silicon solar panels is uniform, the current distribution is more uniform, and the probability of hot spot effect is lower. The hot spot effect refers to the fact that during the operation of the solar panel, due to local shading or differences in the performance of the cells, the temperature of some cells is too high, thereby affecting the performance and life of the entire solar panel. Due to the non-uniformity of the grain boundary, polycrystalline silicon solar panels are more prone to current concentration, and the hot spot effect is relatively more obvious.
(IV) Power attenuation and service life
The power attenuation rate of monocrystalline silicon solar panels is relatively low, usually 0.3% - 0.5%/year, and the component life can reach more than 30 years. Its stable crystal structure and high-quality materials ensure the power generation efficiency in long-term operation. The annual attenuation rate of polycrystalline silicon solar panels is generally between 0.5% and 0.8%, and the component life is 20-25 years. Although polycrystalline silicon solar panels have cost advantages in initial investment, the performance degradation in long-term operation may affect their overall economic benefits. When selecting solar panels, it is necessary to comprehensively consider the expected operating cycle of the project and the long-term return on investment to determine the more suitable product.
III. Cost
(I) Production cost
The production process of monocrystalline silicon solar panels is complex, requiring high-purity silicon materials and precise temperature control, and the energy consumption in the production process is high, so the production cost is relatively high. The manufacturing process of polycrystalline silicon solar panels is relatively simple, with lower requirements for silicon material purity, high material utilization rate in the production process, and low energy consumption, making its production cost about 10%-20% lower than that of monocrystalline silicon solar panels. With the continuous advancement of technology and the advancement of large-scale production, the production costs of monocrystalline silicon and polycrystalline silicon solar panels are gradually decreasing, but there is still a certain gap between the two.
(II) Levelized cost of electricity (LCOE)
The levelized cost of electricity is an important indicator to measure the economic feasibility of solar power generation projects. It takes into account factors such as the initial investment of solar panels, operation and maintenance costs, power generation, and the time value of money during the project life cycle. Although the initial investment of monocrystalline silicon solar panels is relatively high, their high efficiency and low attenuation rate make the cost per unit of power generation (LCOE) advantageous in long-term operation. In areas with sufficient sunshine, monocrystalline silicon solar panels can recover their investment in a shorter period of time and achieve higher economic benefits. Polycrystalline silicon solar panels have a certain appeal in short-term projects or scenarios with limited budgets due to their low initial cost, but due to their relatively low efficiency and high attenuation rate, their LCOE may be higher than that of monocrystalline silicon solar panels in the long run.
IV. Application scenarios
(I) Application scenarios of monocrystalline silicon solar panels
Projects with limited space: such as urban rooftop photovoltaic systems, commercial building integrated photovoltaic solutions, etc. Due to the high conversion efficiency of monocrystalline silicon solar panels, more electricity can be generated in a limited space to meet users' demand for power generation.
High-end market and projects with high requirements for appearance: The surface of monocrystalline silicon solar panels is uniform dark blue or black, and the corners are often rounded. The appearance is beautiful and the visual effect is more modern. It is suitable for high-end residences, villas or commercial projects pursuing green building certification. It can not only achieve efficient power generation, but also enhance the overall image of the building.
High temperature areas and areas with complex lighting conditions: Monocrystalline silicon solar panels have good high temperature performance and strong weak light response ability. In hot desert areas, tropical climate areas or northern areas with insufficient light, they can maintain good power generation performance and ensure the stable operation of solar energy systems.
Long-term investment projects: For investors who pursue long-term stable returns, the low attenuation rate and long life of monocrystalline silicon solar panels enable them to continuously generate stable electricity during the life of the project, providing a more reliable return on investment.
(II) Application scenarios of polycrystalline silicon solar panels
Large-scale ground photovoltaic power stations: In areas with sufficient land resources, the low cost advantage of polycrystalline silicon solar panels makes them an ideal choice for large-scale ground photovoltaic power stations. Although its conversion efficiency is relatively low, it can achieve considerable power generation and reduce unit power generation costs by laying over a large area.
Projects with limited budgets: such as rural photovoltaic poverty alleviation projects and distributed power generation projects in developing countries. These projects are usually sensitive to initial investment. The economic efficiency of polycrystalline silicon solar panels can meet their needs for realizing solar energy utilization under limited budgets.
Areas with complex environments but not severe obstruction: Polycrystalline silicon solar panels are slightly more adaptable to local obstruction. In some dusty or occasionally obstructed areas, even if some cells are affected, the loss of overall power generation efficiency is relatively small, and the normal operation of the system can still be guaranteed.
Short-term return projects: For some projects that hope to quickly recover investment costs, the low initial investment of polycrystalline silicon solar panels can reduce the financial pressure of the project and achieve profitability in the short term.
V. Market trends and technological development
In recent years, with the continuous innovation and advancement of technology, the market share of monocrystalline silicon solar panels has gradually expanded. On the one hand, the continuous breakthroughs in monocrystalline silicon N-type cell technology (such as TOPCon and HJT) have further improved the conversion efficiency and continuously improved its cost performance. On the other hand, large-scale production and process optimization have led to a continuous decline in the production cost of monocrystalline silicon, and the cost gap with polycrystalline silicon has gradually narrowed. At the same time, policy guidance has also promoted the development of monocrystalline silicon solar panels. Countries have introduced policies to encourage the development of clean energy and provide more support for high-efficiency photovoltaic technology, making monocrystalline silicon solar panels occupy a more advantageous position in market competition.
However, polycrystalline silicon solar panels are also constantly developing and improving. Some manufacturers have developed high-efficiency polycrystalline products, such as cast monocrystalline, through technological innovation, trying to narrow the performance gap with monocrystalline silicon. In certain specific markets and application scenarios, polycrystalline silicon solar panels still have certain market demand due to their cost advantages, especially in developing countries and cost-sensitive projects.
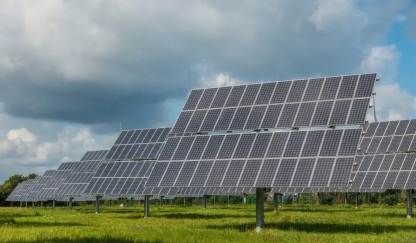
As a professional solar panel manufacturer, Ningbo Sun Earth integrates R&D, manufacturing and sales, and creates efficient and reliable photovoltaic products with advanced technology and strict quality control. Sun Earth use automated production lines and international standard testing processes to ensure that each solar panel has excellent power generation performance and a service life of more than 25 years.
Core advantages
✔ Efficient power generation: using advanced battery technologies such as PERC and TOPCon Module, the module conversion efficiency is leading in the industry
✔ Stable and durable: passed multiple harsh environmental tests such as anti-PID, anti-salt spray, and anti-wind pressure
✔ Intelligent production: digital control of the entire process to ensure product consistency and yield
✔ Customized service: special components such as different powers, sizes and BIPV can be provided according to needs
Sun Earth solar panels have been widely used in household roofs, industrial and commercial power stations, photovoltaic poverty alleviation and other projects, and have won the trust of customers at home and abroad with excellent quality. Choosing Sun Earth Solar means choosing a long-lasting and efficient green energy solution!
Keywords:
Sun Earth Solar, Ningbo Sun Earth, Sun-Earth, Sun Earth, TOPCon Module, solar panels,